My blower was manufactured by the Kinetic Blower Company of Hagerstown, Maryland. If I'm interpreting the tag correctly, it puts out 5" static wind pressure and delivers 500 cubic feet per minute. By all my calculations that should be plenty. It has a 3/4 h.p., 110 v., single phase motor.
I built a rack for holding both the blower and reservoir, the reservoir above and the blower below. The reservoir is as close to the ceiling as possible so the wind trunk can be as short as possible. (Reservoir details in the next post). The blower is as close to the reservoir as possible to avoid drawing in cold basement floor air. It also prevents any dampness from getting to the blower. The blower is mounted on rubber vibration isolating grommets and the connection to the reservoir is padded with thick foam rubber. I don't want any vibrations coming up from the blower to the living room. Probably overkill, but I wanted to be sure.
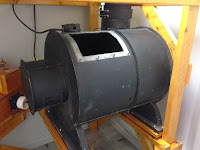
I became a bit concerned about it though when I had it set up for testing. It seemed to get rather hot, and it had a heck of a time recovering after I played a big chord. The motor and impellers are both enclosed inside a shell with just a little access panel. It was hard to read anything on the motor itself or get in there to service it. I asked about the overheating on the DIYapason list and someone suggested I make sure the motor is turning the right direction. I thought it odd that it might be in there backwards, but that would explain the lack of wind and over heating. I opened the access door and turned it on momentarily. Sure enough, it was going backwards! This particular motor has a shaft going out each end, so it was an understandable mistake. I tried finding the little electrical box so I could switch the wires and turn it the other way, but I couldn't find it. So, I took the whole thing apart to turn the motor 180 degrees. (It turns out the electrical box was covered by the impeller). Once I had the motor out of the housing and removed the impellers, I noticed it was turning really hard by hand- it felt like a bearing was going out. Since I had it apart, I decided it was time to take it in. Fuller Electric Motor Service in Lincoln quickly determined that yes, there was a bearing going out and that was the real reason for the overheating. They replaced both bearings, installed a new capacitor, replaced a broken safety switch, and replaced a rubber mount. They also gave it a good cleaning. They said the motor is probably over 50 years old, but built like a tank. Definitely worth repairing. Now it is ready for another 50 years of service. I put it all back together and now it can run for an hour and barely gets warm.
Blower Album