Windchest Part 1:
Design & Layout
I am presenting the construction of my two-rank windchest in 4 parts because it would be horribly long to do it as one post. It is still horribly long. But then, it was a really big undertaking. I began this last summer and worked on it off and on until now. I wanted to wait until it was pretty much done before posting anything. That's why there hasn't been much activity on this blog this winter, even though I have been working away in the shop. Plus, this lets me organize it in more chronological order- I actually skipped around a bit when working on it. Even though this is a blog format, I posted these in reverse order so they should show up on your screen numbers 1-4 as you scroll down. Start here and keep reading:
From the start of this whole project, I had the opportunity to add one rank of pipes, possibly two if I wanted a Celeste. None of these extra pipes were included with my initial purchase, nor was a windchest included to play them. After deciding to add a Rohrflöte and String Celeste I began searching for an appropriate chest. I wanted a two-rank chest, "A" layout (largest pipes in the center), electro-pneumatic (EP) action, and absolutely no more than 85 inches long. Oh- and it had to be within a day's drive of Lincoln so I could go pick it up. I posted a want-ad on churchorgantrader.com and other websites and checked eBay daily for almost a year with no luck. What are the chances of finding a used chest exactly as I wanted? Slim. I thought about building a Direct-Electric (DE) chest because it would be easier and quicker than EP. On the other hand, it would cost more money and I wasn't too fond of having two types of action in the same instrument.
A couple years ago, I was talking to Fred Zander (then at Bedient Organs) about replacing a few water damaged pouches in my existing chest. I mentioned my search for the ideal EP chest and my plan to just build a DE chest instead. He really didn't like the idea of mixing the actions either. He pointed out that building EP chests isn't all that difficult, as long as a person's woodworking skills are precise. It would take more time, yes, but it would be better to have the whole organ on EP action.
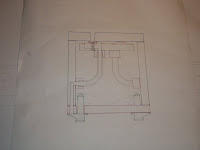
This past summer, I began designing the chest. I knew the basic dimensions, but I hadn't the foggiest idea about how to design the action. The Organ Supply Industries catalog shows a couple general styles, but no details or construction diagrams. I called Fred and we met to discuss my project and he graciously offered me some insights and advice. We looked at both OSI styles and I decided to go with Style 2, in which the pouch well is connected to the magnet port via a piece of vinyl tubing and a boring in the sidewall of the chest. I had measured the pipe toe openings, and from that calculated the diameter of each toe hole in the chest (chest hole should be about 1.5 times the diameter of the pipe toe hole). Fortunately, the toe holes were all small enough that I not only didn't need to use primary valves, but all of the pouches could be the same size as well. That made things a lot simpler. We decided to use a 7/8" valve on a leather pouch 2 1/4" diameter covering a pouch well 1 3/4" diameter by 9/16" deep. Armed with this knowledge, I sat down to draw out the chest.
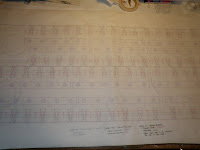
As a landscape designer, I have plenty of drafting paper lying around, so I drew everything out at actual size. I decided to build two matching but separate chests (one for each rank) rather than one big chest. Being my first windchest, I thought that might be a bit more manageable. The spacing of the smaller treble pipes was dictated by the size of the pouch and well. The spacing of the larger tenor pipes was dictated by the diameter of the pipes themselves. I didn't want to waste any space, but the pipes couldn't bump shoulders either. I am an old-school draftsman preferring to work with pen and paper instead of CAD, so I started with one sheet showing the pouch wells and added layers of opaque vellum over the top showing leather pouch placement, toe boards, and rack boards. Then I added layers under it showing the tubing manifolds, bottom boards, and magnets (shown above right). I also drew a 1:1 scale drawing of the chest in cross section (shown above left). Remember- you can see a whole album of photos by clicking on the link at the end of each posting.
Now that I had blueprints, I called Fred and he ordered the leather pouches & fish glue for me from Columbia Organ Leathers. I then bought premium poplar and plenty of 32-pair cable from Bedient. The best lumber was used for the pouch boards, second best for the toe boards, and good quality lumber for the side and bottom boards. One of the members of my church has a very nice wood shop with a planer and he let me come by to plane the rough lumber down to the appropriate thickness.
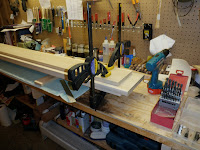
Now it was time to lay everything out. I cut the pouch board, toe board, and rack board to the exact length. Each board received a thorough sanding. I then positioned one atop the other precisely as they would be in the finished chest and clamped them together. Although the long pouch boards would each be cut into three sections, I decided to leave it as one for now to improve the accuracy of my layout. On the top of the rack board I marked the toe holes and rack pin holes. On the bottom of the pouch board I marked the mounting screw holes and guide dowel holes. Then I screwed the three together so I could drill the pilot holes. I drilled the toe hole pilots through the rack board and toe board and barely into the pouch board. This ensures that the rack board hole is perfectly in line with the toe board, which is perfectly in line with the pouch and valve below. I did the same with the markings on the bottom board, but only drilled into the toe board, not the rack board. I drilled a 1/4" hole through the pouch board and into the toe board. This will hold a dowel that will ensure that the pouch board is mounted precisely in place under the toe board.
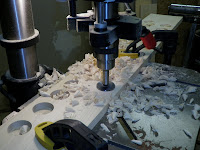
Next, I unscrewed the three boards from each other so I could drill the pouch wells. My pilot bit wasn't long enough to all the way through the pouch board, so I started by continuing the pilot holes all the way through. I then used a 1 3/4" Forstner bit to bore the pouch well because this type of bit is capable of boring large holes with perfectly flat bottoms. The pouch wells were bored 9/16" (14mm) deep. Next, I turned the pouch board over and drilled a 3/8" hole through the center of each well. This hole will be used to center the pouch when laying it, but then also receive the spring that raises the pouch up after playing.
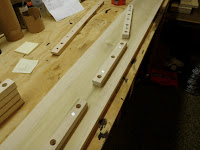
The next step was to layout, cut, and attach the tubing manifolds. These manifolds hold the vinyl tubing in place under the pouch board and against the side board. I cut each manifold and glued on a cork gasket before screwing it to the under side of the pouch board (or onto the side board). This ensures that the well's exhaust port is perfectly aligned with the hole in the manifold, which is perfectly aligned with the vinyl tubing. Same with the side board manifolds. Returning to the pouch boards, I drilled a 3/8" hole through the bottom of the well and half-way through the manifold. When all had been drilled, I removed the manifolds and drilled a pilot hole the rest of the way through the manifold. I then drilled a 9/16" hole from the opposite side going just over half-way through. This hole receives the vinyl tubing, and the 3/8" hole lines up perfectly with the inside of the tubing. On the side boards, I attached the manifolds and drilled a pilot through the manifold and just deep enough into the side board to mark it. I then removed the manifolds and drilled a 3/8" hole from the side board side and a 9/16" hole from the vinyl side. I re-attached the manifolds and drilled a 3/8" diameter hole 9/16" into the side board.
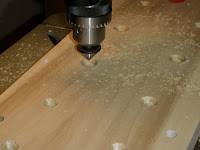
Then, I turned my attention to the toe boards. I wrote each toe hole's diameter on the toe board in millimeters. Millimeters are much easier to work with than 32'nds of an inch. I was sure to drill from the inside out because I wanted as clean and crisp of a hole as possible where the valve seats against the toe board. If there was tear-out on the top of the board (and there was), it isn't a big deal because most of the tear-out was removed by chamfering the toe holes. If the chamfer didn't get it all, it still wouldn't affect the pipe speech. I also drilled the holes to receive the rack pins and I drilled the pilot holes for attaching the toe board to the side boards. Next, I used a large countersink bit to cut the chamfers in the toe holes. This sunken, beveled edge seats the pipe foot over the toe hole.
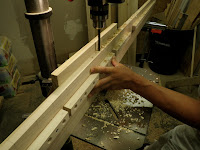
The last step in this phase was drilling the hole through the side board connecting the vinyl tubing with the electro-magnet in the bottom board. I made a fence to attach to the drill press table, holding the sideboard centered exactly below the drill bit and holding it at a right angle. With some precise marking, these holes lined up perfectly with the holes going from the vinyl, through the manifold, and into the side board.
Design & Layout Album
No comments:
Post a Comment